

Simulation setup and run: At this point you define in fine detail the properties of all the fluids, solids and boundaries and define what kind of solver you want to use during the simulation, incompressible flow, compressible flow, steady solution, dynamic solution heat transfer and so on. Please have a look to this site to have a good introduction to the meshing. Choice of the grid dimension is not trivial and once again a preliminary study can give some information, for example if our simulation aim to study a boundary layer to have an estimation of layer thickness can aid to choice a proper grid dimension. Unfortunately the accuracy of the simulation result is dependent on the mesh geometry itself.
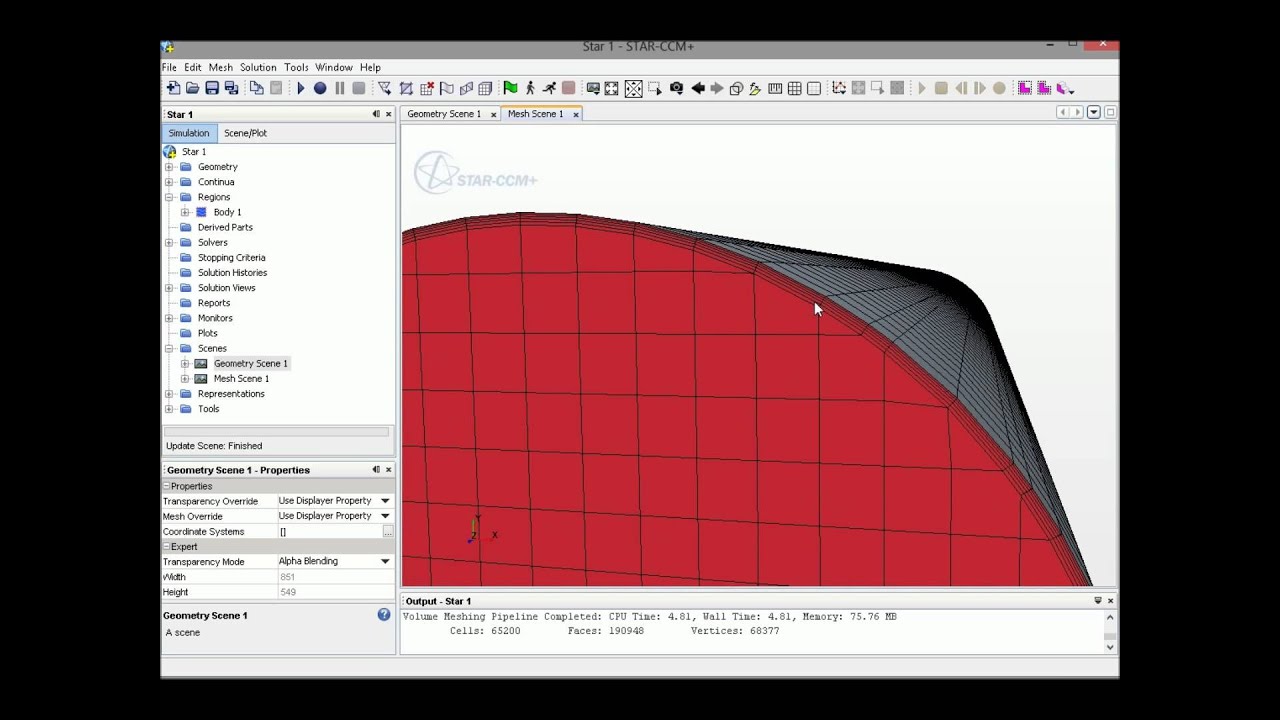
Mesher must also divide the simulation physical domain into a discrete grid, in a CFD problem the physical variables are calculated, for example, on the vertex of the grid. This features will be used during the simulation setup phase to define fluids, solids and boundary conditions properties. Meshing: Mesher must add simulation related information to our model, the model should be divided in regions and surfaces, for the mesh to be usable all the boundaries relevant to the physical problem must be identified.
#Pipe flow m file software#
Geometric modeling phase: Here a 3D or 2D model of the case to be simulated is drawn, no matter what software or format you use as long as it is easy to pass the data to the mesher software. Study phase is fundamental to check simulation results. For example a simplification can regard a geometric complexity reduction or the decision to neglect thermal transfer equations, both the cases can yield to a dramatically reduction of modeling, meshing and simulation time. With the preliminary study done it is possible to individuate the assumptions and simplifications that can be acceptable. Preliminary study phase: It is necessary to study the problem analytically, in such a way the sought test cases are individuated.

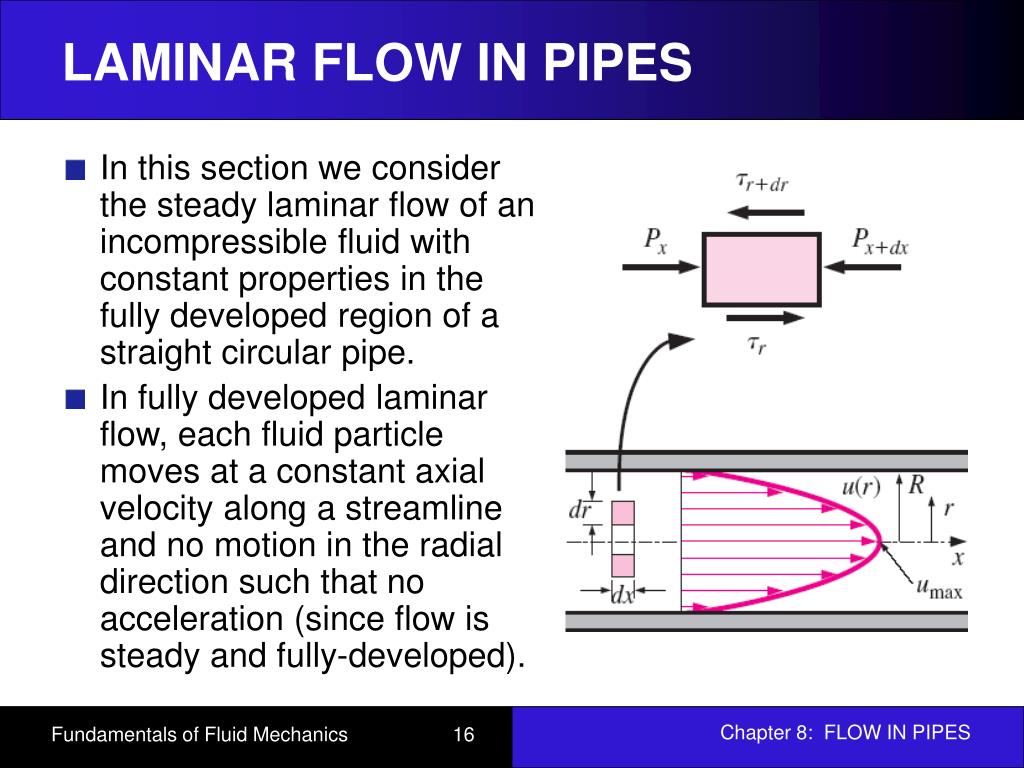
Goal of the example is to compare analytical results with CFD results.Īll the files needed for the example Elmer CFD can be downloaded here. With an adequate calculation power it’s possible to estimate position error for a particular aircraft and instrument.įor the sake of simplicity the problem solution with CFD techniques is split into six main subproblems that are defined here below after general concepts a numeric example is inspected.
#Pipe flow m file free#
CFD commercial codes, and other needed software to complete the toolchain is not in typical DIY maker budget range, hence the numeric example will be carried out using the free and well proven package Elmer CFD.Īt a glance, returning to our typical basic air data problem, CFD can calculate the velocity, pressure, temperature and density field for our given geometry and so derived standard defined aerodynamics parameters as the lift and the drag. There are many CFD commercial packages available, as well as a lot of well documented simulation cases, just to stay in topic have a look to the pitot simulation here. Nowadays there are some free CFD software at home maker disposal, the calculation power of personal computers is enough to reasonably cope with CFD design tasks. Computational fluid dynamics is a versatile and powerful tool, nevertheless it’s scarcely used in DIY applications.
